Page 4 of 4
Re: Kyosho Rocky 4wd..... I think?
Posted: Thu Sep 08, 2016 10:08 am
by GoMachV
3D printed parts are cool for some things but you really need to make them bulky to be durable. If you go the 3D printed route, I'd beef it up using all the space you have available to you
You might try to use a piece of aluminum drilled for the pivot and steering link, and insert the ball joint ends perpendicular to the piece. That keeps the same geometry and also keeps it simple while still durable.
This is what I'm trying to convey- even tho I drew the servo link end on the wrong side lol
Re: Kyosho Rocky 4wd..... I think?
Posted: Thu Sep 08, 2016 4:14 pm
by Antonov
Comment noted. I don't have any 3D print experience! But I think we might be able to make something looking right AND robust. A friend of mine proposes to print in ABS but if required nylon (he has access to such printer). For trials, that should do the job.
Once we have something nicely designed, I will see if it needs to be reinforced and/or printed in some other materials?
On the other side, breaking a "printed" part is not such a drama cause reproductible at low cost on a push of a button !
And then I can save the genuine original bellcranks to avoid killing rare parts...
Re: Kyosho Rocky 4wd..... I think?
Posted: Fri Sep 09, 2016 1:58 am
by Antonov
GoMachV wrote:
This is what I'm trying to convey- even tho I drew the servo link end on the wrong side lol
Looking at your suggestion twice... I think the idea to turn 90° the ball joint is a good idea to limit the space taken by the part. But on the other side, it does create a weakness in the sense that it is made to push / pull in the axle of its length = the screw thread. Doing it this way would tend to pull on the side when turning or bumping hard. Maybe that would be so short that it would have no concrete impact on strength. I would try

Re: Kyosho Rocky 4wd..... I think?
Posted: Fri Sep 09, 2016 9:34 am
by Antonov
Something like this ?
Beefy.
Delrin open ends perpendiculary to the arm. But you see, I am not sure that would be strong enough caused by the 90° torque from the wheels pushing the Delrin on their sides... knowing that there is not MUCH space to drill in the threads for those two... not sure it is the best setup.
Re: Kyosho Rocky 4wd..... I think?
Posted: Fri Sep 09, 2016 11:43 am
by Antonov
I would prefer do the "bulky" version as you advise but with lateral open-ends, pushed into the arm and screwed on a common thread axle.
Re: Kyosho Rocky 4wd..... I think?
Posted: Sat Sep 10, 2016 10:30 am
by AscotConversion
Why not a sedan style rack with the ball horizontal? This isn't a drop in solution, but the general design idea might work. Moving the chain guide back might help, if that would fit.
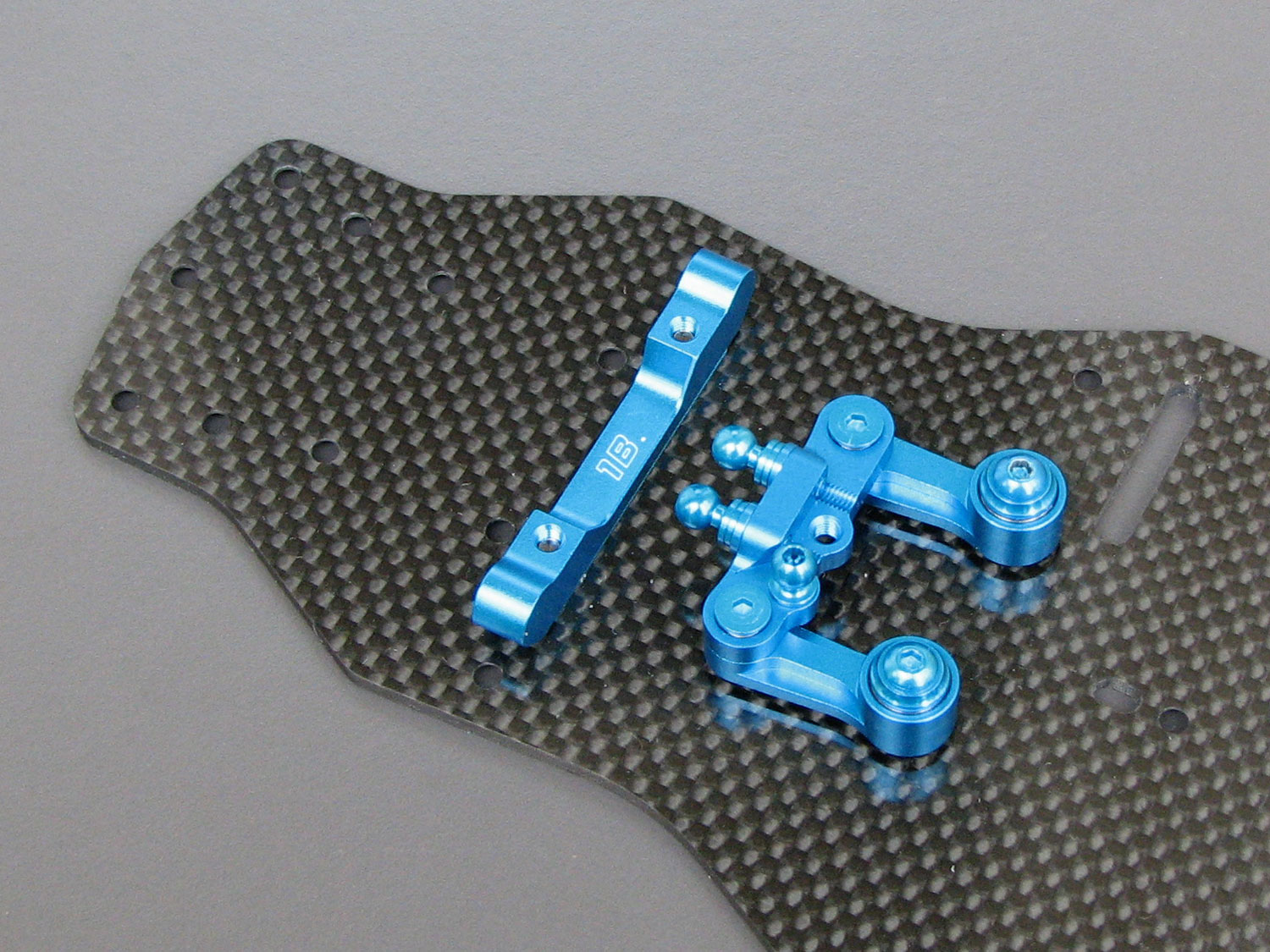
Re: Kyosho Rocky 4wd..... I think?
Posted: Sat Sep 10, 2016 7:01 pm
by Phin
A Winning Edge Pro-Steer style rack and pinion set-up could work.
For something modern though rocker arms from a Tamiya TA06 or 3Racing F1 suspension could be modded into bellcranks.
Re: Kyosho Rocky 4wd..... I think?
Posted: Sat Sep 10, 2016 7:26 pm
by GoMachV
The crank has a weird swoop to it, making most bellcranks incompatible. It would take one that droops a good 1/4" or so. Adding to that there is no room for a conventional ball joint and it becomes even harder. A pro steer idea is good, but lacking a lot of clearance to fit it. An alien mid setup might be closer lol
Re: Kyosho Rocky 4wd..... I think?
Posted: Sat Sep 10, 2016 7:58 pm
by Phin
On the rocker arms, the ball studs don't stand up like conventional cranks...they're laid down like on the bellcranks AscotConversion posted. Don't have any to give measurements but they don't look much wider than 1/4". Maybe 7-8mm.
http://www.rcmart.com/tamiya-54313-ta06-aluminum-rocker-p-34075.html?cPath=595_744_1527
Re: Kyosho Rocky 4wd..... I think?
Posted: Tue Sep 13, 2016 2:43 am
by Antonov
Hello, that's interesting.
On the other hand, it looks like nothing "perfect" exists and whether the case, would not be an easy fit. Then I still continue to think that a 3D printed part would be the best option: so cheap to produce (about than 1 $ each) with a design that can be just perfect is the engineering is properly done.
Just yesterday, I was in a RC shop for some tiny missing part on my yellow Rocky and the guy just show me how his 3D printer was working. The parts he makes are pretty impressive: amazingly resistant (I was just astonished how hard and resistant they are), rigid and the finishing itself improved a lot: it is not a baby skin surfacing but it is much better than just what it was one year ago.
So I will keep you posted but that might be really the best option.